常见的质量缺陷
1.收缩裂纹和裂缝
2.蜂窝和麻面
3.孔洞和缺棱掉角
4.均质性差,存在强度隐患
收缩裂纹和裂缝
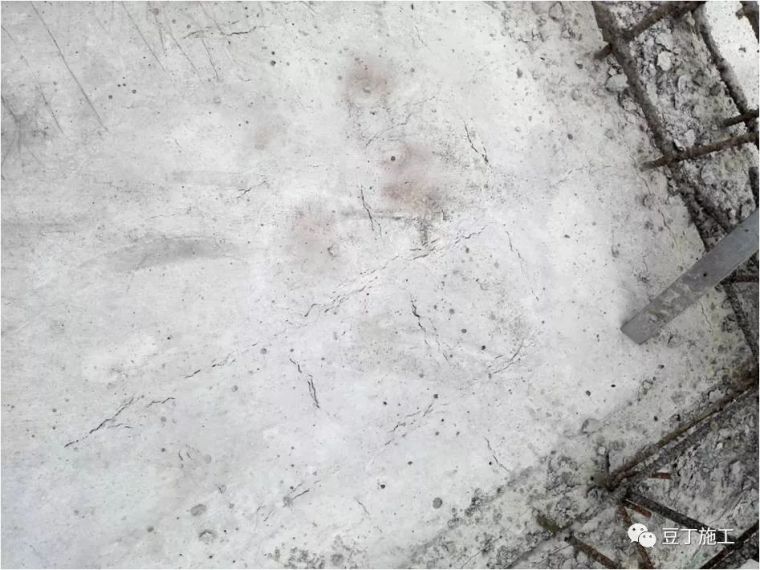
产生原因分析:混凝土初凝时间较长,自身收缩较大,加之钢筋保护层厚度局部小于5cm,产生矩阵型的收缩裂纹。
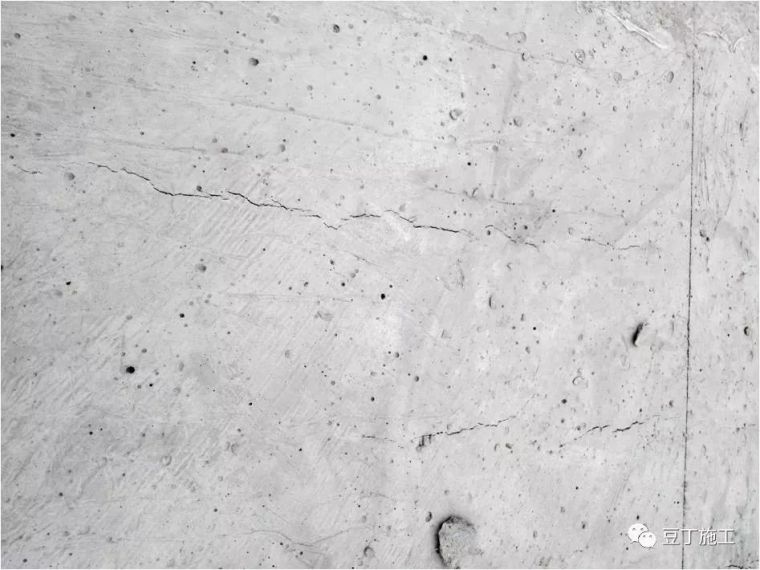
产生原因分析:覆盖薄膜后,混凝土和薄膜之间有泌水产生隔离,薄膜起不到作用,产生收缩裂纹,且没有进行二次抹面。
预防措施:
1、在混凝土初凝后,可以站人但表面还能产生鞋印的情况下,进行二次收面,大范围采用抹面机,预埋钢筋和模板夹角处采用手工抹面。
2、终凝后及时覆盖养生土工布,并洒水,洒水程度土工布湿润脚踩有水挤出即可,常规每2~4个小时洒水一次,根据天气情况,让土工布一直保持湿润就满足要求。
蜂窝和麻面
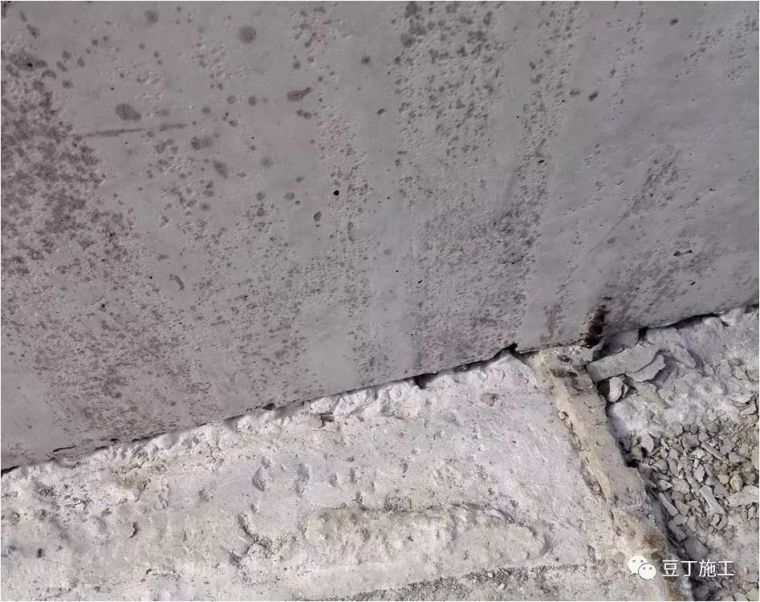
产生原因分析:混凝土和易性不良且存在过振现象,造成离析产生蜂窝和孔洞。
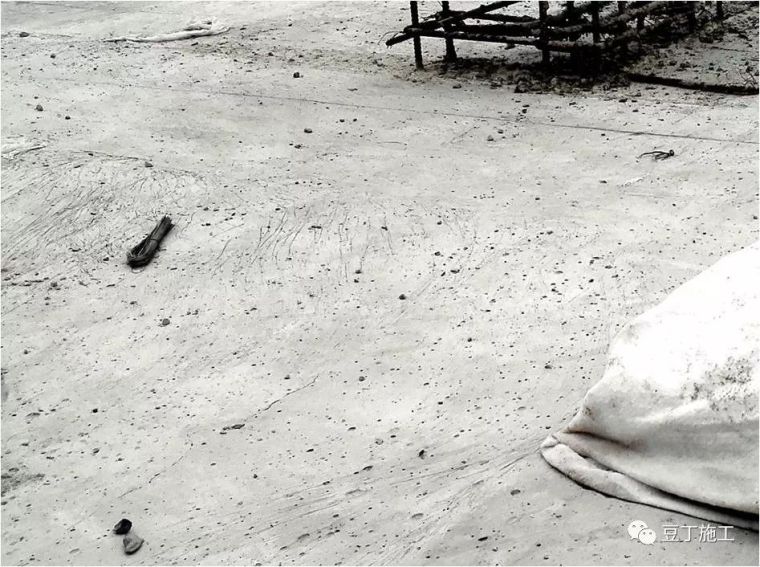
产生原因分析:混凝土刚刚振捣完毕,在气泡没有完全上浮完成时就覆盖了薄膜,且薄膜与混凝土面密贴较好,气泡在混凝土表面成气孔。
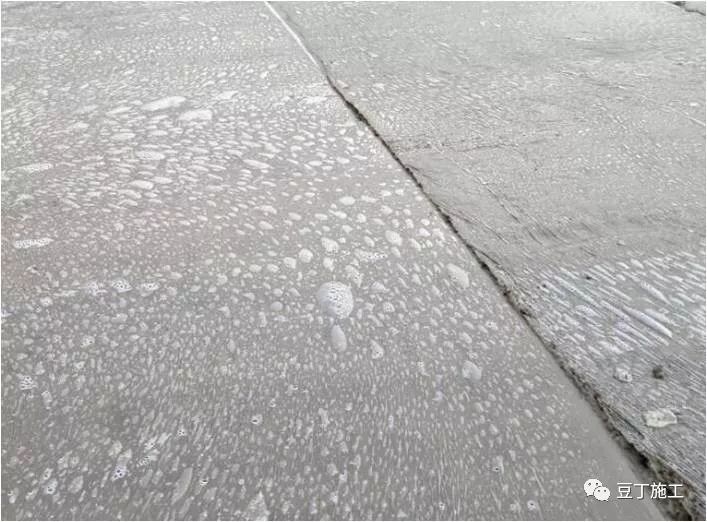
混凝土振捣完成,在气泡上浮过程中覆盖薄膜产生的气包,且没有进行二次收面,这是产生表面麻面的主要原因。
预防措施及方法:
1、表面尽量使用坍落度较小的混凝土。
2、混凝土振捣密实以后,间隔20分钟左右的时间再覆盖薄膜,覆盖前确定表面没有泌水,且要进行收面。
3、初凝后,掀开薄膜观察,有蜂窝和麻面的再次进行一次抹面。
孔洞和不规则接茬
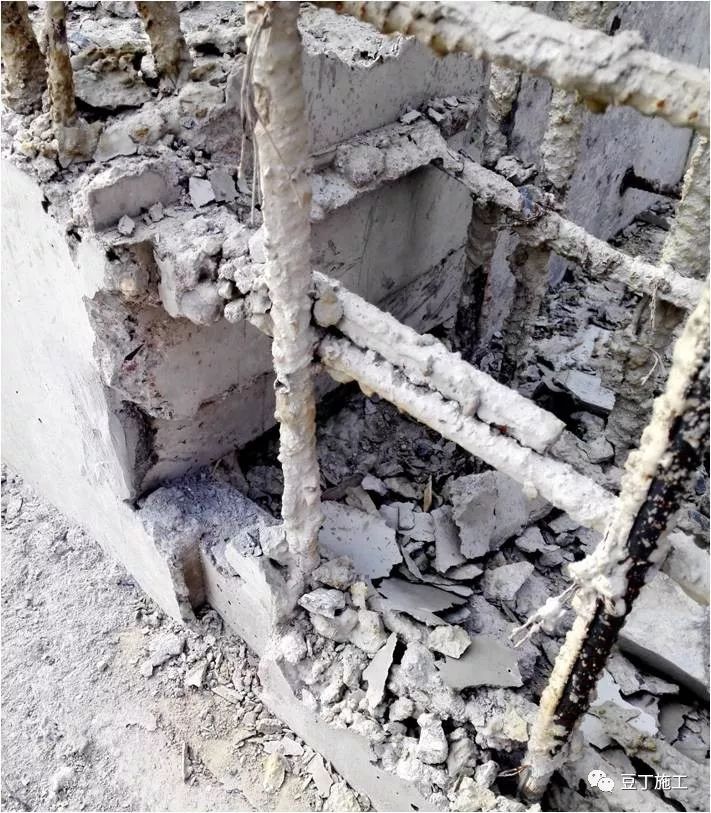
产生原因分析:模板加固不严谨,有跑模现象,布料随意,振捣随意,模板漏浆造成混凝土不成形,不规则,不但实体质量有隐患,接茬不利,外观质量也很差。
预防措施:
1、布料要均匀,特别是在外墙设有止水钢板的位置。
2、振捣要把控好,不可过振,也不可漏振,在夜间施工时,准备好手提照明设备。
3、混凝土初凝后,及时剔除布料时撒在模板以外的混凝土和振捣后跑出模板以外的混凝土。
均质性差,存在强度隐患
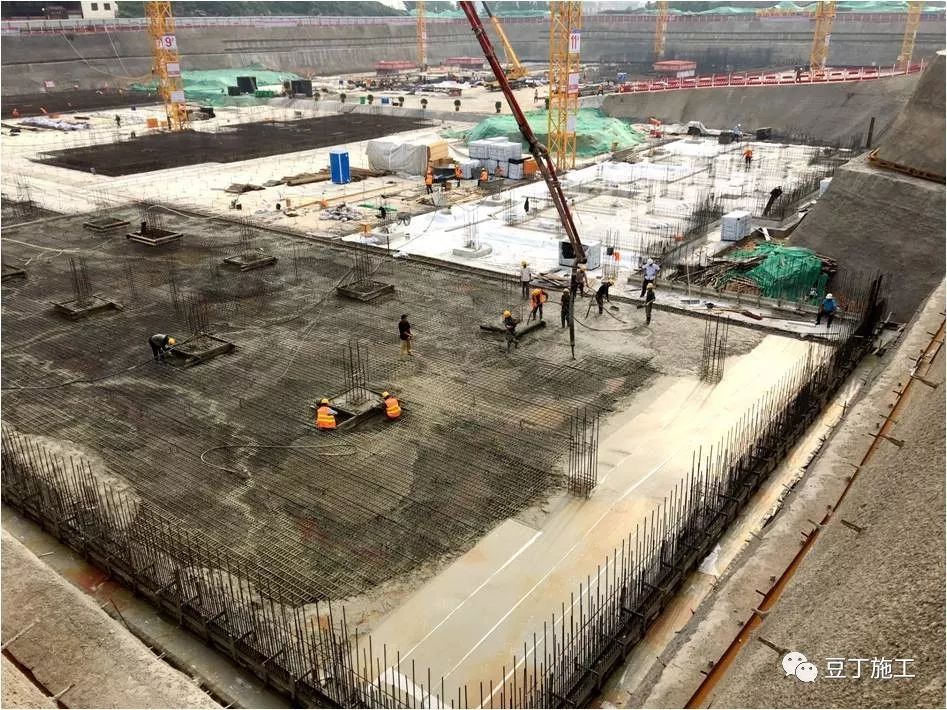
第一种情况:
满铺第一层,在浇筑第二层时,第一层已经初凝,易产生分层,对混凝土的整体性有很大的影响。
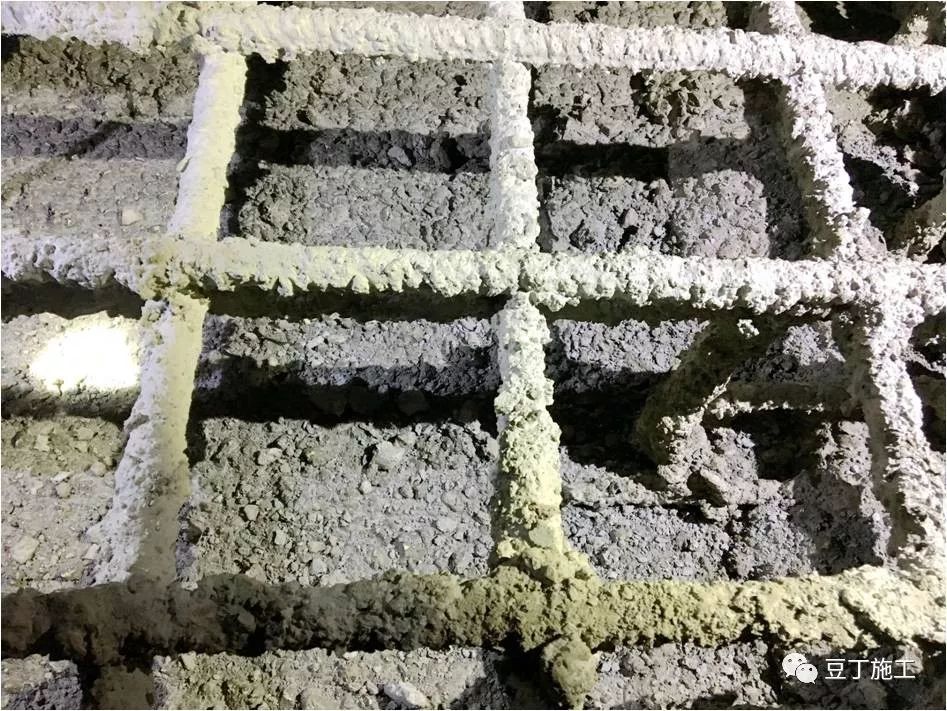
第二种情况:
与第一种情况相同,且布料随意,没有章法,随意性强。再者混凝土到场太慢,凝固时间较快,一般4小时内即终凝。
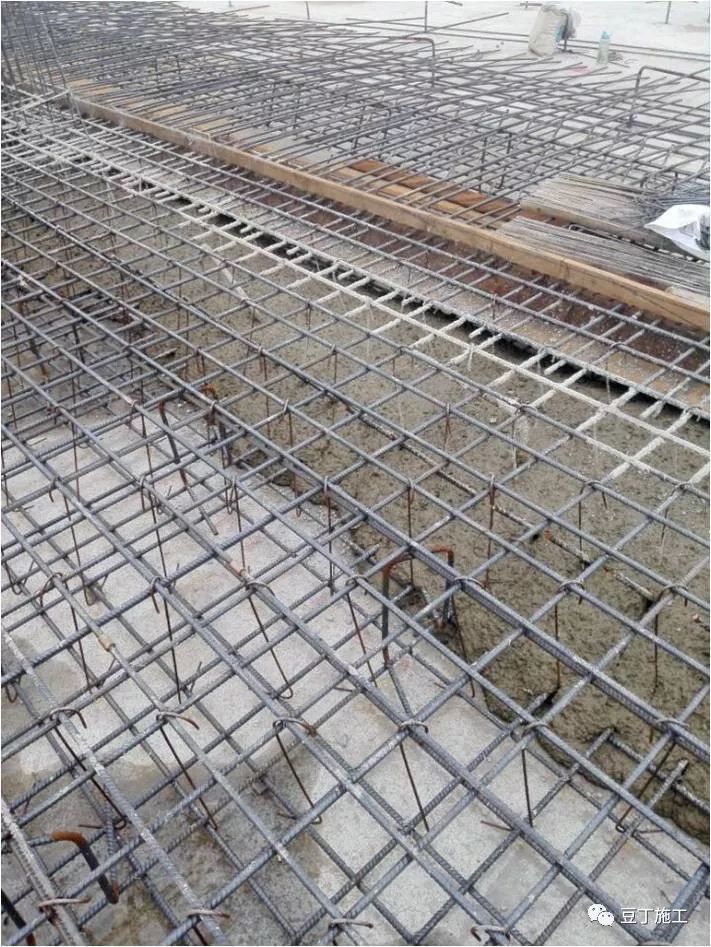
第三种种情况:
在伸缩缝周围先进行封边,且有的部位产生漏振,待上部混凝土再浇筑时,封边混凝土已经终凝。
产生原因分析:
1、大体积混凝土使用一台泵车相对来说不能满足浇筑要求。
2、混凝土凝固时间与常规小体积混凝土相同,相对于大体积浇筑来说,略快。
3、布料顺序太随意,没有章法,未按照交底要求台阶法分层浇筑。
4、现场管理不到位,操作人员较少,一班人疲劳作业,消极对待。
措施1
条件允许的情况下,采用双泵车,或1台泵车加一台地泵,并专人负责混凝土的联系,确保混凝土能及时供应。
措施2
严格执行台阶分层浇筑法。
台阶分层浇筑,即浇筑前根据浇筑厚度和宽度计算分台阶的长度,如从一端开始向另一端以台阶分层法浇筑,就要计算分层的长度,比如一块筏板高1.2m,宽15m,长50m,那可以最大分3层,每层40cm厚,每个台阶长度按5m计算的话,就是0.4×15×5=30m³,约2车,浇筑时间25分钟,时间上很合理,看演示图。
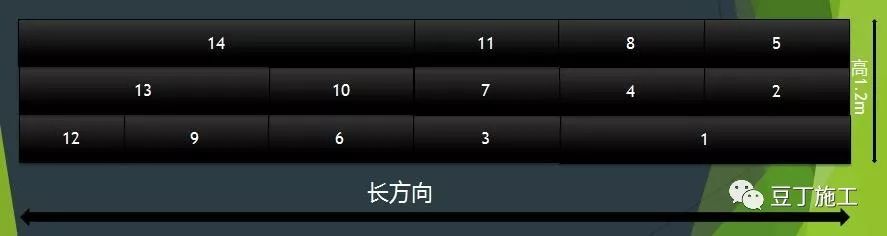
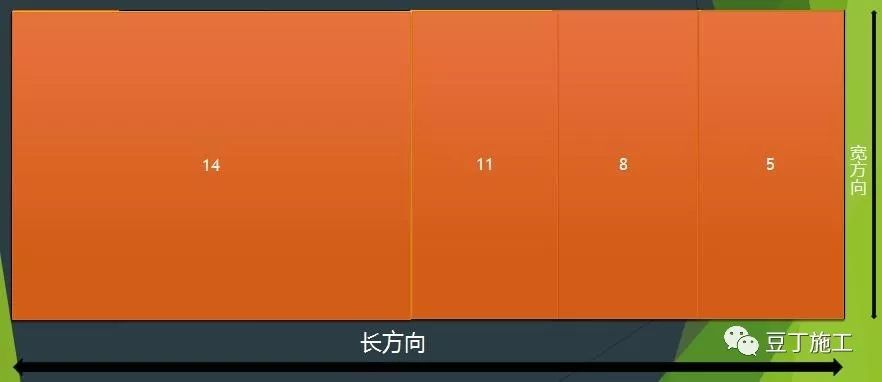
措施3
现场组织能力须加强,配足人员,不论是一班人打到底还是分两组轮休,最起码的布料手2人、振捣手2人,振捣助手2人,收面2人绝不能少。在此基础上,现场班组长还要负责对周边模板和混凝土情况进行巡视,确保混凝土不漏,不涨模,不漏振,不过振。